Japanese Sword Polishing: The Craft and Its Importance

What’s in this article?
The Japanese sword is renowned for its artistic blade features, which can be fully appreciated after a skilled polisher has meticulously polished it. A sword polisher enhances the beauty of the blade, refining its final shape, color, and texture. Traditional schools of polishing have even developed techniques to bring out the sword’s finest qualities.
Let’s delve into the importance of sword polishing, what makes a good polish, and the Japanese techniques of the craft.
Why Is Polishing Crucial to Japanese Swords?
Traditionally-made Japanese swords, or nihonto, feature artistic details on the blade surface. These include the hamon (temperline pattern), the jihada (grain pattern), and the jigane (steel surface). Polishing brings out all these features necessary for the aesthetic appreciation of Japanese blades. A polished blade also helps identify the blade’s smith or school and allows careful examination in sword appraisal.
A Japanese blade has a good polish when all its artistic features are distinctly visible. On the contrary, a poorly polished blade may have a seemingly clean surface, yet its details remain obscured, making a careful examination impossible.
Polishing also enhances the functionality and effectiveness of a blade. A polisher puts a sharp cutting edge on the blade, whether newly made or requires repairs for nicks or deformities. In fact, several flaws on the blade surface—as long as they are not fatal—can be fixed by polishing. Polishing also gives the blade a reflective, mirror-like finish. Still, some old swords remain cloudy even when polished.
Types of Finish Polish
Traditionally-made Japanese blades go through meticulous polishing methods. The two primary types of finish are the hadori and sashikomi.
Hadori
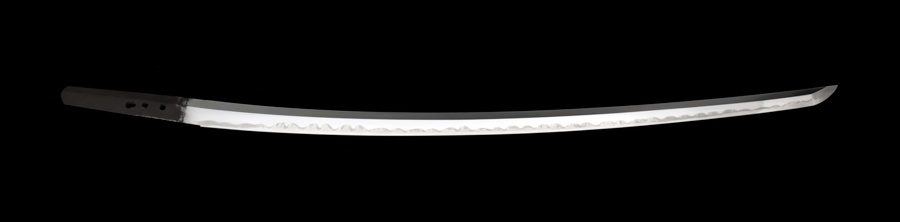
The process of whitening the hamon (temperline pattern) area is called hadori. Many sword collectors today favor a pronounced hamon, and the hadori enhances its visibility and brilliance. It creates more contrast between the white edge and the dark body of the blade, further accentuating its visual appeal.
The hadori (刃取り) is also known as kesho (化粧), meaning cosmetic. It is relatively new and does not predate the Meiji era. Generally, the polisher decides how close he follows the habuchi or nioiguchi—the boundary defining the hamon. Unfortunately, the whitening effect of the hadori masks these finer details of the steel.
Many sword connoisseurs more interested in metalwork and craftsmanship sometimes forgo the hadori process in polishing. Still, if the hadori is done correctly, all details of the hamon, including its habuchi and activities (hataraki), can be visible in the close examination.
Sashikomi
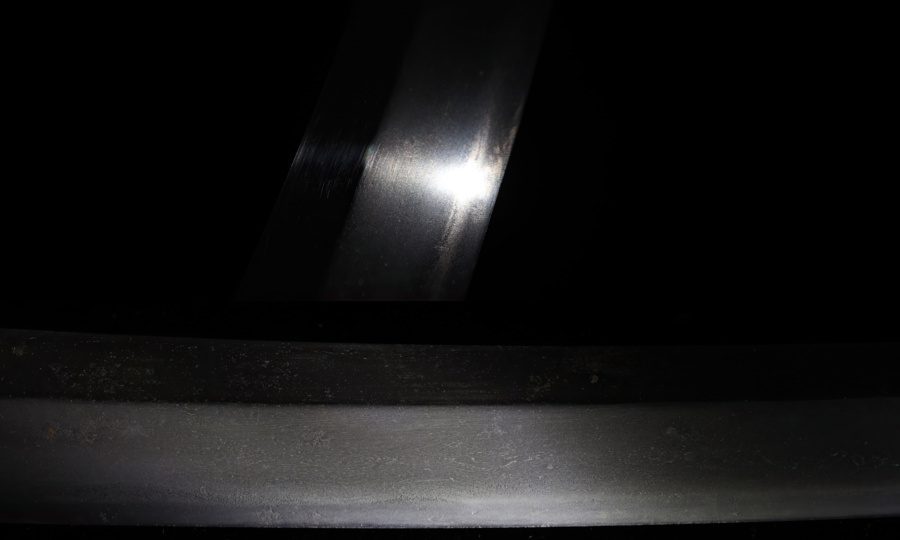
The sashikomi (差し込み) is the traditional form of polishing before the hadori became popular. However, its effects can look a bit subdued. It shows the details of the entire blade but does not particularly emphasize the hamon against the blade’s body. Instead, it shows the hamon with all the details of its structure.
Polishing Techniques of Japanese Swords
Polishing a newly-made Japanese blade is as complex as making it. It involves two main processes: foundation polishing (shitaji togi) and finish polishing (shiage togi). Throughout these stages, traditional polishing stones of varying coarseness shape and refine the blade.
Shitaji Togi: The Foundation Polishing
During the shitagi togi stage, the polisher shapes the blade, refines it, and prepares the surfaces for finish polishing. The polishing stones used include the arato, kongoto, binsui, kaisei, chu-nagura, koma-nagura, suita, uchigumori-hato, and uchigumori-jito.
The foundation polishing aims to make the blade’s surfaces even, such as keeping the ridge line (shinogi) formed correctly. This process also sharpens the cutting edge and reveals the hamon (temperline pattern) and jihada (grain pattern).
Shiage Togi: The Finish Polishing
During the shiage togi stage, the polisher enhances the color and appearance of the blade’s surface. The aim is to make the artistic details more visible, define a sharp point (kissaki), and attain a mirror-like finish. For this, thin shavings of polishing stones, backed with paper and lacquer, are used.
Using Hazuya Stones
The hazuya stones remove the scratches, marks, or blemishes from the previous polishing stage. They are used on the cutting edge and the hamon, excluding the point area. At this point, the surface of the blade should be uniform and smooth.
Utilizing Jizuya Stones
The jizuya stones enhance the appearance of the blade’s surface and make the jihada (grain pattern) stand out. This process contributes to a darker and more distinct overall appearance.
Applying Nugui Solution
A mixture of iron oxide and clove oil, known as nugui, is applied to the blade’s surface. It gives a non-reflective, darkened finish to the steel. However, too much nugui will turn the metal black. The darker surface enhances the visibility of the jihada and other intricate details.
Whitening the Hamon
A hadori stone whitens and enhances the visibility of the hamon (temperline pattern), giving it a strong contrast against the blade’s body.
Defining the Point
The point (kissaki) of the blade is the last to be polished. It involves two processes: the sujikiri and narume. The sujikiri process creates the yokote line—or the line defining the point from the blade’s body. The narume process, on the other hand, polishes the point area, ensuring clarity in the boshi (the hamon pattern in the point area).
Burnishing the Blade Surface
The burnishing process, known as migaki, creates a mirror-like finish on the mune (back surface) and shinogi-ji (upper surface above the shinogi ridge line). It uses a burnishing needle (migaki-bo) and spatula (migaki-bera).
History of Japanese Sword Polishing
In the early days, Japanese swordsmiths not only crafted the blades but also polished them to acquire sharp cutting edges and refine their final shape. However, as time passed, a specialization in sword polishing emerged, leading to separate artisans dedicated solely to this craft.
Kamakura Period (1192 – 1333)
During the Kamakura period, sword polishers began to work independently from the swordsmiths. Their skills advanced to the point where they could effectively polish blades, revealing the artistic details on their surface.
Muromachi Period (1338 – 1573)
Professional sword appraisers started to emerge in Japan. Samurai swords were increasingly valued not only for their functionality as a weapon but also for their artistic qualities. As a result, the techniques and expertise in polishing continued to develop during this period.
Edo Period (1603 – 1867)
Sword polishing and appraisal had become highly sought-after among the ruling shogun and daimyo. The demand for Japanese swords was driven not only by their practicality but also by their status as symbols of power, prestige, and refined craftsmanship.
Facts About Japanese Sword Polishing
Japanese sword polishing, known as togi, is vital to the sword making process. A sword polisher who refines a Japanese blade is called togishi. Sword polishers bring out the beauty of a blade and highlight the sword’s important appraisal points. They also refine the blade’s shape and make sharp cutting edges.
After forging the steel into a blade, the swordsmith passes it to the polisher for further refinement.
A polisher first refines the blade’s geometry, including its lines and surfaces. Then, the polisher sends the blade to a habaki maker, who fits the blade collar to the tang. After that, the blade is transferred to a scabbard (saya) maker to provide a sheath that fits the blade’s exact measurement. Finally, the blade returns to the polisher for final polishing, bringing out the jihada (grain patterns) and the hamon (temperline pattern).
Japanese blades that have undergone numerous polishing are referred to as tired.
Swords can be described as thin or thick, with the thickness of the blade referred to as kasane. Blades that have retained their original thickness are often described as “healthy” or “robust.” However, blades that have undergone multiple polishing sessions are considered “tired” due to the decreased thickness resulting from the removal of metal during the polishing process.
Some flaws on the surface of the blade can be fixed by polishing.
A sword polisher can remove some flaws on a blade if they are not considered fatal. For instance, a polisher may reshape the kissaki (point) if it has a broken tip as long as the hamon remains intact. Unfortunately, when the hamon is interrupted, a polisher cannot fix the damage. Such flaws are fatal, called kizu, which diminish the value of a Japanese blade.
Polishing stones are the traditional and primary tools used to polish swords.
In Japan, polishing stones are mined from the Kyoto mountains. They have an extraordinarily fine grain and are extremely expensive. In ancient times, polishing stones were prized gifts offered among feudal lords.
Polishing stones play a crucial role in revealing the full potential of a blade’s steel surface, known as jigane. Various stones will interact with steel differently, and each blade will require a slightly different stone to highlight its beauty.
A sword polisher’s apprenticeship can last up to ten years.
Making a Japanese sword requires the skills of several highly specialized artisans. Sword polishers can apprentice for 5 to 10 years, depending on the school, while swordsmiths apprentice for 5 to 7 years before acquiring licensure. Also, a habaki (blade collar) maker trains for up to 8 years before being able to stand on his own. As a result, their works are highly honored and sought-after.
Apart from swords, other bladed weapons also undergo polishing.
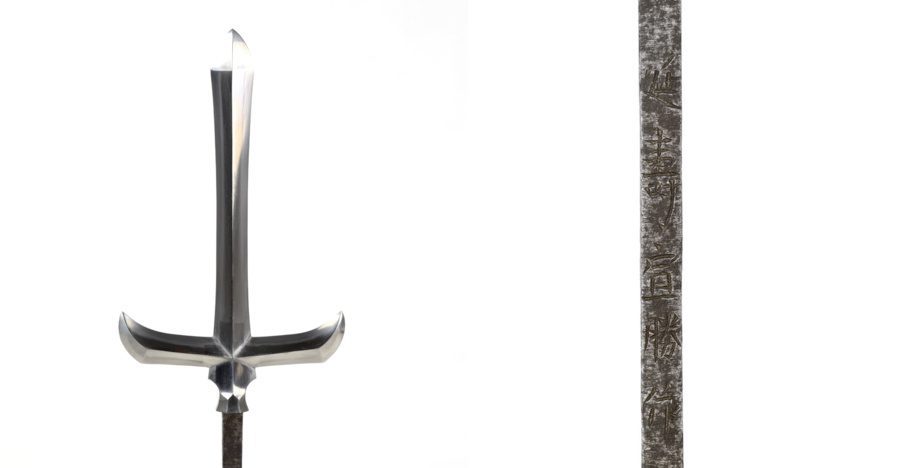
The Japanese katana sword and wakizashi are widely known and appreciated, but the polishing craft extends beyond swords. The tanto dagger, Japanese spears (yari), and other bladed weapons also received polishing to enhance their functionality and appearance. Polishing removes imperfections and sharpens the blade, enhancing its cutting ability.
Conclusion
Polishing allows the intricate details of the Japanese swords to be fully appreciated. A swordsmith can spend an enormous time forging a blade, but a sword polisher’s craftsmanship is crucial in preserving the sword’s historical and cultural significance. Good polishing allows a functional, beautiful sword to be treasured for generations.